National Cold Headers (Cold Parts Formers) for Operators
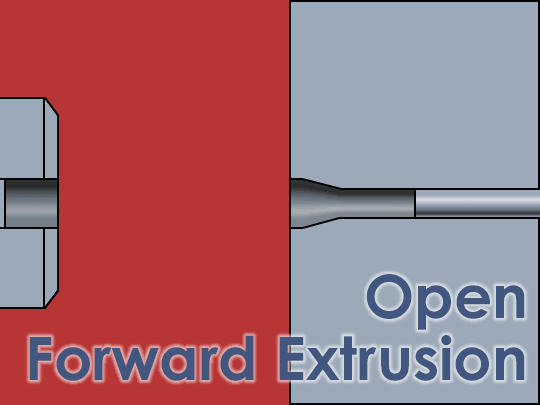
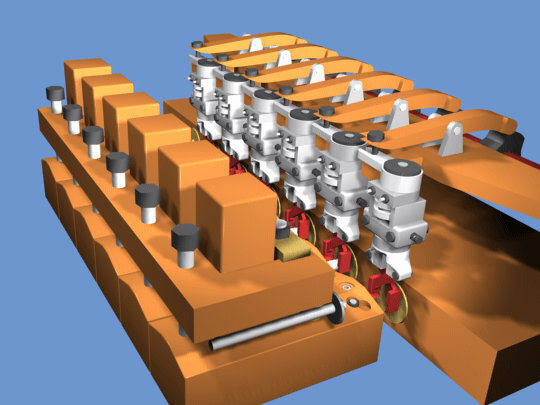
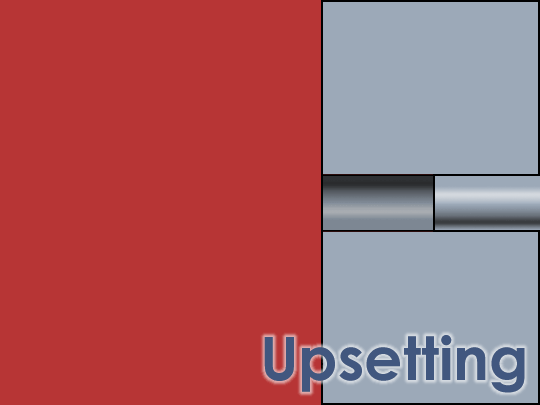
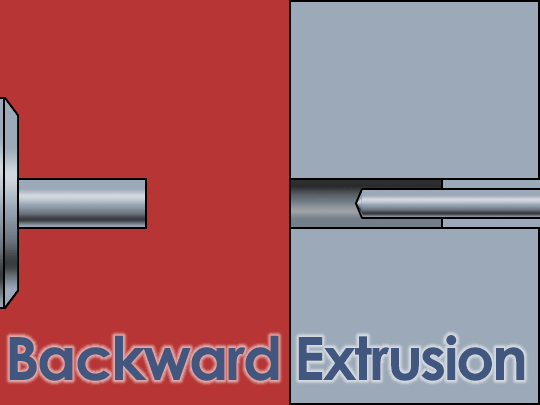
Cold parts formers use a series of dies to hammer sections of metal cut from a roll into finished parts. The part is cut, and then passed from die to die with arms. The shape changes in each die. The process is very fast, extremely loud, covered in oil, and occurs behind a protective shield, so it’s difficult to observe what the machine is doing directly.
New operators were challenged in understanding how the machine was working, and this made things like changeovers and troubleshooting even more difficult for them. And that lack of understanding directly led to more downtime for the machines.
The training portion leveraged 3D animation to open up the machine and show the process and components clearly, quickly showing how basic the machines actually are. Training also covered basic operation, startup, and shutdown. The EPSS walked through the details of changing the tooling of a machine over for a different part, troubleshooting, and maintenance.
On this program I worked as PM and ID. I conducted the FEA, scoped and managed the budget/timeline, conducted all onsite research, developed the design document/content, and storyboarded the lessons. Boards were handed off to a graphic artist for 3D modeling, animations, and illustration, and to a developer who built the program in Authorware.